In fact, it is a CNC milling machine. It is called a "CNC machining center" in Guangzhou, Jiangsu, Zhejiang and Shanghai. It is an automated machine tool equipped with a program control system. (Numerical control machine tool) is the abbreviation of Computer numerical control. An automated machine tool controlled by a program. The control system can logically process programs with control codes or other symbolic instructions, and decode them by a computer, so that the machine tool can operate and process parts. The rough material is processed into semi-finished finished parts by cutting tools.
CNC Machining (CNC Machining) refers to processing with CNC machining tools. CNC index-controlled machine tools are programmed and controlled by CNC machining languages, usually G codes. The CNC machining G code language tells the Cartesian position coordinates of the machining tool of the CNC machine tool, and controls the feed speed and spindle speed of the tool, as well as the tool changer, coolant and other functions. Compared with manual machining, CNC machining has great advantages. For example, the parts produced by CNC machining are very accurate and repeatable; CNC machining can produce parts with complex shapes that cannot be completed by manual machining. Numerical control machining technology is now widely promoted. Most machining workshops have CNC machining capabilities. The most common CNC machining methods in typical machining workshops are CNC milling, CNC lathe, and CNC EDM wire cutting (wire electric discharge). The tools for CNC milling are called CNC milling machines or CNC machining centers. The lathe that performs numerical control turning processing is called a numerical control turning center. CNC machining G code can be programmed manually, but usually the machining workshop uses CAM (Computer Aided Manufacturing) software to automatically read CAD (Computer Aided Design) files and generate G code programs to control CNC machine tools.
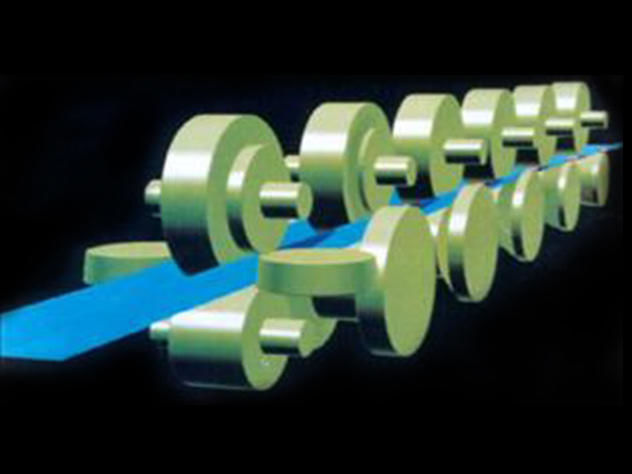
CNC machining has the following advantages:
① The number of tooling is greatly reduced, and complex tooling is not required for processing parts with complex shapes. If you want to change the shape and size of the part, you only need to modify the part processing program, which is suitable for new product development and modification.
②The processing quality is stable, the processing precision is high, and the repeat accuracy is high, which is suitable for the processing requirements of the aircraft.
③The production efficiency is higher in the case of multi-variety and small batch production, which can reduce the time of production preparation, machine tool adjustment and process inspection, and reduce the cutting time due to the use of the best cutting amount.
④It can process complex profiles that are difficult to process by conventional methods, and even process some unobservable processing parts.
The disadvantage of CNC machining is that the cost of machine tools is expensive and requires a high level of maintenance personnel.